Visiting the aircraft manufacturing factory: Uncovering the story behind the bir
2024-07-01 / tech
The maturation of advanced composite materials technology has made it possible to achieve optimal performance and low cost, thereby greatly promoting the application of composite materials in aircraft. Some major aircraft manufacturers are gradually reducing the proportion of traditional metal processing in aircraft design and manufacturing, and are giving priority to the development of composite material manufacturing. This article aims to introduce the main processes and advanced specialized equipment involved in the manufacturing process of composite materials.
1. Application of Composite Materials in Aircraft
With the development of composite material manufacturing technology, the amount and application areas of composite materials in aircraft have become one of the important indicators to measure the advancement of aircraft structure. The trends in the application of composite materials in aircraft are as follows:
(1) The use of composite materials in aircraft is increasing day by day.
The amount of composite materials is usually represented by the percentage of the aircraft's structural weight they occupy. Major aviation manufacturing companies around the world are showing an increasing trend in the use of composite materials. The most representative are Airbus's A380 and the subsequent A350 aircraft, as well as Boeing's B787 aircraft. The A380 has about 30t of composite material. The B787 has a composite material usage of up to 50%. The A350 aircraft has an even more record-breaking 52% composite material usage. The use of composite materials in military aircraft and helicopters also shows the same increasing trend, and the rapidly developing unmanned aerial vehicles (UAVs) in recent years have pushed the use of composite materials to a higher level.
Advertisement
(2) The application is developing from secondary load-bearing structures to primary load-bearing structures.
Initially, composite materials were used to manufacture secondary load-bearing structures such as aircraft doors, fairings, and stabilizers. At present, composite materials have been widely used in primary load-bearing structures such as the fuselage and wings. The extensive application of composite materials in primary load-bearing parts has greatly improved the performance of aircraft, and the economic benefits brought about are very significant, which also promotes the development of composite materials.
(3) The application on complex-shaped structures is becoming more and more widespread.The use of composite materials to manufacture complex curved components on aircraft is also increasing, such as the fuselage sections and spherical rear pressure bulkheads on the A380 and B787 aircraft, which are all made using fiber placement technology and resin film infusion (RFI) processes.
(4) The complexity of composite material components has increased significantly, with large-scale monolithic and co-curing molding becoming the mainstream.
The most direct effect of the extensive use of composite materials in aircraft is weight reduction. Composite components made with co-curing and monolithic molding techniques can form large-scale monolithic parts, significantly reducing the number of parts, fasteners, and molds, and minimizing part assembly, thereby effectively reducing manufacturing costs.
(5) Manufacturing methods for composite materials and advanced specialized equipment have seen rapid development and widespread application.
Traditional composite material manufacturing technologies have a low level of automation, leading to unstable quality of composite components, large variability, poor reliability, and high production costs, making it impossible to produce large and complex composite components. The continuous increase in aircraft structural sizes has made the manufacturing process of large-sized composite components extremely important.
In recent years, a variety of manufacturing technologies with higher levels of automation have emerged, such as fiber placement, resin film transfer molding/infusion molding, and electron beam curing. Along with these, advanced, efficient, and low-cost specialized equipment has been developed and industrially applied, such as three-dimensional weaving machines, fully automatic tape laying equipment, and tows placement equipment. These efficient automated equipment have significantly improved the production efficiency and internal quality of composite materials, reduced costs, and made it possible for composite materials to achieve optimal performance and low cost simultaneously.
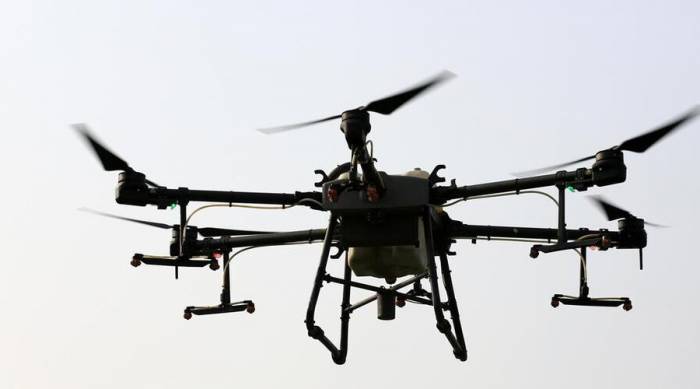
2. Composite Material Manufacturing Processes and Key Equipment
The molding of composite materials is a relatively complex process. With the emergence of various new processes and technologies, composite material manufacturing processes have become the key to the processing and manufacturing of composites, covering a wide range of technical aspects, high technological content, and accounting for more than 80% of the total cost.According to different requirements such as application, volume, and market, the molding processes for aerospace composite material products have adopted technologies such as manual lay-up, semi-automatic molding, fully automatic molding, and liquid molding. The following is a focused explanation of the main process methods and equipment involved in production.
(1) Manual lay-up.
At present, manual lay-up is still a widely used traditional molding method, and even the manufacturing of products like the B-2 bomber and some general aircraft involves a large number of manual lay-up processes. This is because the order quantity of these products is often in the single digits, while the quality requirements are very high. The advantage of the manual lay-up method is that it allows for significant changes in the thickness of the skin, local reinforcement, embedding of metal reinforcement plates for joints, and the formation of reinforced ribs and honeycomb sandwich areas, etc.
Currently, manual lay-up employs many specialized equipment to control and ensure the quality of the lay-up, such as automatic cutting and feeding systems for composite prepreg and laser positioning systems for lay-up. That is, specialized numerical control cutting equipment is used for the flat cutting of prepreg and auxiliary materials, thus transforming the manufacturing process that depends on the production of templates into a manufacturing process that can be fully operated according to data files generated by composite material design software.
The disadvantage of manual lay-up is that it requires the lay-up personnel to have very high skills and construction experience. Manual laying is labor-intensive and time-consuming, therefore it has low efficiency and high cost (accounting for 1/4 of the total cost), and it is difficult to meet the production requirements of large-scale production and large, complex composite material components. Therefore, in the early 1960s, after several years of implementation of manual lay-up composite materials, automatic tape laying (ATL) technology was developed.
(2) Automatic Tape Laying (ATL).
Automatic tape laying technology uses unidirectional prepreg tape with a release paper, and its cutting, positioning, laying, and rolling are all automatically completed using numerical control technology, realized by an automatic tape laying machine. A multi-axis gantry mechanical arm completes the automatic control of the tape laying position, and the tape head is equipped with a prepreg tape conveying and cutting system, which automatically completes the laying of the prepreg tape and the cutting of specific shape positions according to the boundary contour of the workpiece to be laid. The prepreg tape is laid onto the mold surface under the pressure of the roller while in a heated state.Automatic tape-laying machines can be categorized into two types based on the geometric characteristics of the parts being laid: flat tape-laying and curved tape-laying. With the further development of automatic tape-laying equipment, programming, computer software, tape-laying technology, and materials, the efficiency of automatic tape-laying has become higher, the performance more reliable, and the operability more user-friendly. Compared to manual work, advanced tape-laying technology can reduce manufacturing costs by 30% to 50%, can form composite parts with extra-large dimensions and complex shapes, and ensures stable quality, reducing the time for layering and assembly, near-net-shape forming of the workpiece, and reducing the consumption of machining and raw materials. Currently, the most advanced fifth-generation tape-laying machine is a ten-axis machine equipped with dual ultrasonic cutting knives and a gap optical detector, capable of laying tapes up to 300mm wide, with a production efficiency dozens of times that of manual stacking.
To form complex double-curvature surfaces, narrow tapes are required, which reduces work efficiency, and the cost of a single tape-laying machine can be from 3 to 5 million US dollars, which is too high. Therefore, Hercules pioneered the development of Automatic Tape Placement (ATP) equipment.
(3) Automatic Tape Placement (ATP).
The Automatic Tape Placement technology combines the advantages of automatic tape-laying and filament winding technology. The tape-laying head integrates the independent delivery of different pre-impregnated tows used in winding technology with the compaction, cutting, and re-feeding functions used in tape-laying technology. The tape-laying head gathers several pre-impregnated tows into a variable-width pre-impregnated tape under a compaction roller, which is then laid on the surface of the core mold. During the laying process, the pre-impregnated tows are heated to soften and compacted to set the shape.
Compared to automatic tape-laying, the automatic tow-laying technology can form more complex structural parts with a lower material consumption rate. It represents the pinnacle of automated manufacturing technology, and the importance of ATP equipment to composite materials is equivalent to the importance of milling machines to metal material structures. It is a layering method between automatic winding and automatic tape-laying, particularly suitable for the manufacture of complex components. The foundation of automatic laying technology lies in the design and development of the laying machine.
Taking the Viper fiber laying system from the American Cincinnati Machine Company as an example, the Viper fiber laying system combines winding, special tape-laying, and computer control to automatically produce complex parts that require a large amount of manual layering, thereby shortening the layering and assembly time. Due to the near-net-shape forming of the workpiece, the consumption of machining and raw materials is reduced.
Worth Company manufactures 23% of the fuselage for the Boeing 787, including 47 sections of 5.8m x 7m and 48 sections of 4.3m x 4.6m, using the Viper6000 automatic tape-laying machine from Cincinnati. During manufacturing, the 3900 series carbon/epoxy non-woven tape from Toray is stacked on a large cylindrical rotating mold, which is composed of interlocking core shafts. After the cylindrical parts are laid, they are placed in the world's largest autoclave with a volume of 23.2m x 9.1m for curing. Currently, automatic tow-laying machines can lay both narrow and wide tows.
Robotic automatic laying of pre-impregnated tows/strips has become a powerful and efficient technology for high-performance fiber-reinforced composite material structures. It is an integrated combination of mechatronic equipment technology, CAD/CAM software technology, and material process technology, including: automatic laying equipment technology, pre-impregnated tow/strip cutting technology, laying CAD technology, laying CAM technology, pre-impregnated tow/strip technology, automatic laying process technology, laying quality control, mold technology, cost analysis and control, and integrated collaborative digital design technology, etc., with the advantages of high efficiency, high quality, high repeatability, and low cost.(4) Autoclave curing and molding.
Autoclave curing and molding is a traditional manufacturing process for aerospace composite structural components. It has the advantages of good product repeatability, high fiber volume content, low or no porosity, and reliable mechanical properties. The main disadvantages of autoclave curing are high energy consumption and high operating costs. Currently, large composite components must be cured in large or extra-large autoclaves to ensure the internal quality of the parts. Therefore, the three-dimensional dimensions of autoclaves are continuously increasing to meet the processing requirements of large-sized composite parts. At present, autoclaves are equipped with advanced heating and temperature control systems and computer control systems, which can effectively ensure uniform temperature distribution in the working area inside the tank, ensuring the internal quality and batch stability of composite parts, such as accurate resin content, low or no porosity, and no internal defects. This is also the main reason why autoclaves have been used to this day.
(5) Composite material liquid molding.
Composite material liquid molding is a very popular process, which is mainly based on resin transfer molding (RTM), including various derived RTM technologies, with about 25 to 30 types. Among them, RTM, vacuum-assisted resin transfer molding (VARTM), vacuum-assisted resin injection molding (VARI), resin film infusion molding (RFI), and resin impregnation molding (SCRIMP) are called the five main RTM molding processes, and they are also the most widely used RTM processes at present.
3. Composite material liquid molding process and main equipment
The advantage of RTM is that the finished product has high damage tolerance, and it can form complex components and large integrated parts with high molding precision and low porosity. The key to RTM molding is to have an appropriate reinforcing preform and a resin or resin film with appropriate viscosity. RTM requires the resin to have a low viscosity value at the injection temperature. The first-generation epoxy resin requires a viscosity of less than 500cps (0.5Pa·s), and in the past, for larger-sized components, the resin viscosity was required to be lower than 250cps (0.25Pa·s). The main equipment for the RTM process is various resin injection machines and integrated sealed molds.
With the continuous innovation of new reinforced material structures, the combination of weaving technology and preforming technology with RTM technology has formed new directions for process development and application. For example, using three-dimensional weaving technology to preform the reinforcing material into a 3D structure, and then combining it with the RTM process, or directly preforming the fiber fabric into the shape of the part through sewing or bonding methods, and then using the RTM process to form composite materials.For instance, EADS Military Aircraft Company manufactures the rear pressure bulkhead for the B787 rear fuselage section. It is a hemispherical integral bulkhead that is inserted between the pressurized fuselage section 47 and the non-pressurized section 48 and tail section. This bulkhead is made using the VARTM (Vacuum Assisted Resin Transfer Molding) process and has dimensions of approximately 4.3m by 4.6m. The Boeing 787 is the first aircraft to feature a composite material rear pressure bulkhead.
The manufacturing of this bulkhead benefits from Cytec's resin film infusion system. The toughened composite material has top-tier flame retardant/smoke/toxicity properties, allowing for the omission of fireproof layers, thus making the structure lighter than those obtained through traditional resin film infusion methods. However, most of the bulkheads in the Boeing 787 fuselage are made using the carbon fiber resin film infusion RFI (Resin Film Infusion) technology. The composite bulkheads are connected to the fuselage skin using carbon fiber composite shear straps. Due to design and cost considerations, a few areas still use titanium and aluminum alloy bulkheads.
(6) Diaphragm forming.
Diaphragm forming was originally a molding process developed for thermoplastic composite materials and was later found to have a wide range of applications for thermosetting composite materials. It has the special effect of preventing fiber slippage and wrinkling during the molding process, making it highly suitable for processing the C-shaped cross-section of the front beam of large aircraft wings. In recent years, this process has been widely adopted for the C-shaped cross-section of the front beam in large aircraft such as the A400M.
To form the C-shaped section, the preform is removed from the tape laying machine and sent to a thermoplastic film forming machine provided by the British company Aeroform for shaping. To facilitate vacuum extraction, the preform should be sandwiched between two Kapton polyimide films provided by DuPont Electronic Technologies in Ohio. A vacuum is drawn between the films, and then infrared heating is applied from above the part until the temperature is raised to 60°C within 1 hour. This ensures that even the thickest section at the root of the beam can be uniformly heated to the same temperature. Then, pressure is slowly applied to the laminate between the two films, forming the inner surface of the beam on a lightweight mold. This C-shaped section can be slowly formed within 30 minutes, after which the Kapton film is removed.
In the ALCAS (Automated Layup and Consolidation for Aircraft Structures) program launched in Europe, this forming method has become a typical process for manufacturing aircraft front beams.
(7) Composite part processing, assembly, and non-destructive testing.
After the composite parts are molded, they require mechanical processing, including dimensional processing and drilling, with a demand for high processing quality. Composite parts are brittle and anisotropic, and conventional processing methods cannot meet the quality requirements for composite processing. Traditional cutting methods have the following disadvantages when processing fiber materials: slow cutting speed and low efficiency; composite parts are prone to deformation, making cutting accuracy difficult to ensure; tools and drills wear and consume quickly when cutting high toughness materials; and delamination damage is prone to occur when processing composite laminates. Therefore, it is required that composite production be equipped with specialized equipment such as large automated high-pressure waterjet cutting machines, ultrasonic cutting equipment, and CNC automated drilling systems to meet the requirements of composite parts after processing, ensuring no delamination wear and compliance with assembly dimensional accuracy.
Large wing skin laminates are generally net-shaped cut using large high-pressure waterjet cutting machines. The world's largest cutting machine has a bed size of 36m by 6.5m, manufactured by Flow International. This abrasive waterjet cutting machine can quickly cut thick laminates without causing overheating, with a cutting speed of 0.67m/min for 25mm thick laminates. For 6mm thin laminates, the cutting speed can reach up to 3m/min, and thick skins can be cut at a speed of 0.39m/min.Ultrasonic cutting equipment applies ultrasonic vibration energy to the cutting tool, effectively separating the boundaries of fibrous materials, thereby effectively solving the problems brought by the aforementioned traditional cutting methods. Ultrasonic cutting technology offers excellent cutting quality, characterized by no burrs, no tool wear, no carbonized materials, low cutting force, less likelihood of layer separation, fast cutting speed, and high precision. It has been widely applied in foreign aviation enterprises.
As the metal structure of aircraft gradually shifts towards composite material structures, the automation of composite material manufacturing becomes increasingly important. High levels of automation in assembly technology are particularly significant. The use of composite materials makes it possible for aircraft structures to adopt large monolithic structural components, such as the final assembly of the 787, which only requires the mating of six major components: the forward fuselage, mid-fuselage, aft fuselage, wings, horizontal stabilizers, and vertical tails. These large monolithic components allow the assembly process to avoid the use of traditional giant jigs, instead favoring more portable tools. The movement of aircraft structural components does not employ gantry cranes.
Flexible assembly, automatic drilling and riveting, and other advanced technologies are integrated into the automatic assembly of large composite components. Aircraft flexible assembly technology takes into account the inherent characteristics of the aviation products being assembled, based on the digital definition of aircraft products. It achieves rapid and precise positioning and assembly of aircraft components through flexible assembly processes, digital assembly techniques, assembly tool design, assembly process optimization, automatic positioning and control technology, measurement, precision drilling, servo control, clamping, etc. This can reduce the variety and quantity of assembly jigs, improve assembly efficiency and accuracy, enhance rapid response capabilities, shorten aircraft assembly cycles, and strengthen the rapid development capabilities of aircraft. It is an advanced assembly technology that can adapt to the requirements of rapid development, production, and low-cost manufacturing, and meets the modular and reconfigurable needs of equipment and jigs. For example, the movement of composite wing components in the B787 has adopted flexible assembly technologies such as automated guided vehicles.
Automatic drilling and riveting machines are widely used in the automatic assembly of large composite components, such as the A380 wing assembly, which employs automated movable drilling equipment. The fundamental difference between these drilling devices and traditional metal material drilling equipment is that, to maintain the structural integrity around the rivet holes, drilling must be done without delamination, hence hole-making generally requires hard cutting tools and a multi-step drilling method. Given the different manufacturing methods of composite materials, their machinability also varies. For instance, woven fabrics with a "cross" pattern are easier to machine than unidirectional fabric tapes, the latter having greater wear force and a higher tendency to delaminate and have issues with uncut fibers during drilling. Therefore, different drilling parameters, materials, and shapes of drill bits should be selected according to the different molding methods of composite components.
Non-destructive testing equipment for composite parts mainly requires the configuration of large ultrasonic C-scan equipment and X-ray non-destructive testing equipment. In addition, laser shearing photography and laser ultrasonic testing are also major development directions.
One of the most important advancements in ultrasonic inspection technology is the development of phased array inspection. Compared to traditional ultrasonic inspection, phased array ultrasonic inspection improves the probability of detection and significantly speeds up the inspection process.
Traditional ultrasonic inspection requires many different probes for comprehensive volumetric analysis, while phased array inspection can achieve the same results with a single multi-element probe. This is because each element probe can perform electronic scanning and focusing, with a time delay in the activation of each element probe. The result is that the incident angle of the synthesized ultrasonic beam can be varied, and the focal depth can also be changed, which means that the speed of volumetric inspection can be much faster than the traditional method. This is because, with the traditional method, the probe must be changed in time, and multiple paths must be transmitted to achieve different incident angles and focal depths. In addition, phased array probes can provide a wider coverage range, thus offering higher production efficiency than traditional probes.
(8) Integrated digital design and manufacturing of composite materials.
The unique process characteristics of composite part forming determine that it differs greatly from metal parts in design and manufacturing, and is more complex.Digital design and manufacturing of composite material components are based on composite design/manufacturing platforms and digital manufacturing equipment for composite materials as the foundation of hardware and software. This approach has transformed the traditional design/manufacturing methods for composite materials, adopting digital formats for comprehensive description and data transfer of products, achieving seamless integration between design and manufacturing.
The integration of composite material design software with existing CAD systems provides a powerful platform for the design and manufacturing of composite components, including four stages: preliminary design, engineering detailed design, manufacturing detailed design, and manufacturing output.
The digital manufacturing process for composite components includes processes such as prepreg cutting, layer laying, and curing. Currently, the digital manufacturing of composite components is mainly reflected in automatic prepreg cutting, laser layer positioning, and automatic fiber laying.
For instance, in the B787 project, composite components were all digitally designed using FiberSIM software, and design data was distributed to global partners, ensuring the uniqueness and accuracy of the composite component data. Due to the extensive use of digital design in the B787, its development cycle was shortened by 3 years compared to the B777.
Digital design and manufacturing of composite components make the implementation of concurrent engineering possible, solving manufacturing issues in the early design stages, greatly reducing workshop modifications and repetitive work. The seamless integration of design and manufacturing data shortens manufacturing time, reduces errors brought by manual programming, and improves component quality.
In conclusion, with the increasing use of composite materials in aircraft, the manufacturing of composite materials has rapidly become a major component of the aircraft manufacturing industry. In the future, more than 50% of the structural components of aircraft will transition from metal to composite materials, making composite manufacturing a fundamental method in aircraft manufacturing. Composite manufacturing processes and specialized equipment are one of the key technologies for advanced composite materials, which are worth investing significant human and material resources for research and development and application. Mastering advanced composite manufacturing technology equates to mastering the advanced manufacturing technology for future aircraft.
Comment