Intelligent process design and its development and evolution
2024-07-15 / tech
```
1. Basic Concepts and Connotations of Intelligent Process Design
1) Basic Concepts of Intelligent Process Design
Process design is one of the main tasks of the technical department in manufacturing enterprises. The quality and efficiency of the design have a significant impact on production organization, product quality, product cost, productivity, and production cycle. Process design is a typical complex problem that includes various functional requirements such as analysis, selection, planning, and optimization. It involves a vast amount of knowledge and information and is closely related to specific production environments, such as air humidity, ambient temperature, and the degree of equipment automation. It also heavily relies on experiential knowledge. The connotation of process design (Figure 1) can be summarized as follows: ① A decision-making process that considers all conditions/constraints in the formulation of the process plan, involving various different decisions; ② An activity that combines manufacturing process knowledge with specific design under the constraints of manufacturing resources in the workshop or factory, preparing its specific operational instructions; ③ A bridge connecting product design and manufacturing.
Figure 1 The Basic Connotation of Process Planning - The Bridge and Link between Design and Manufacturing
Computer-Aided Process Planning (CAPP) is a technology where process personnel apply information technology, computer technology, and intelligent technology to transform the product design data of the enterprise into product manufacturing data. Its main features include: it can help process design personnel reduce a large amount of tedious repetitive work, focusing their main efforts on the research and development of new products, new technologies, and new processes; it can enhance the inheritability of processes, achieve the maximization of existing resource utilization, and thereby reduce production costs; it can enable process planners with less experience to complete high-quality process plans, achieving the goal of alleviating the heavy design tasks in the manufacturing industry.
Advertisement
With the continuous maturity of computer software and hardware technology, the theory and methods of computer-aided process planning have made a qualitative leap. Applying artificial intelligence theory to computer-aided process planning is one of the recent research hotspots and is also a development trend in the modernization of process design. It not only transplants research results in the field of artificial intelligence to computer-aided process planning but also expands the application field of artificial intelligence, achieving a perfect combination of the two and promoting their common development.
```Intelligent process design, based on the traditional definition of CAPP, must fully encompass two aspects: first, the explicit, procedural, and modular nature of the process design flow; and second, the intelligent, closed-loop nature of the process design activities. Combining the concept of traditional computer-aided design, the concept of intelligent process design can be summarized as: creating a virtual entity of the process design process in a digital manner, utilizing technologies such as intelligent sensing, cloud computing, big data processing, and the Internet of Things to achieve perception of historical and real-time process design data and knowledge. With the aid of computer software, hardware technology, and support environments, it simulates, verifies, predicts, decides, and controls the design process through numerical calculations, logical judgments, simulations, and reasoning. This forms a closed-loop from "data perception - real-time analysis - intelligent decision-making - precise execution" for the entire design process of a part from rough to finished product, ultimately achieving the intelligent, real-time, explicit, procedural, modular, and closed-loop nature of process design.
2) The Connotation of Intelligent Process Design
In the field of mechanical manufacturing, the use of computer technology is very common. As it has progressed, the originally independent computer-aided design (CAD) and computer-aided manufacturing (CAM) have gradually merged. Computer-aided process planning emerged during the effective integration of the two. Traditional computer-aided process planning technology has the following functions: first, inputting valid design parameters into the computer; second, determining the process flow, basic operations, and related tools applied in the mechanical manufacturing process; third, clarifying the cutting parameters in mechanical manufacturing; fourth, calculating the financial investment and time used in mechanical manufacturing; and fifth, displaying related design data. Intelligent process design is the result of the transformation from the "traditional experience-based design model" to the "science-based design model based on modeling and simulation." The combination of virtual prototyping technology and system simulation methods can not only leverage the predictive capabilities of simulation tools but also integrate the experience of process personnel into the simulation process to conduct various simulation analysis activities during the process design.
Intelligent process design aims to achieve digitalization of processes, flexibility in production, visualization of processes, integration of information, and autonomy in decision-making as its core goals. It revolves around intelligent equipment based on the Internet of Things, intelligent design, intelligent manufacturing, and data integration platforms for process design. Its basic functional system and technology can be represented as:
(1) Control Module. The control module, which is the main control module of the system, is responsible for integrating other modules of the system, providing the system's interface for external access, and completing effective communication and transmission of information between various modules.
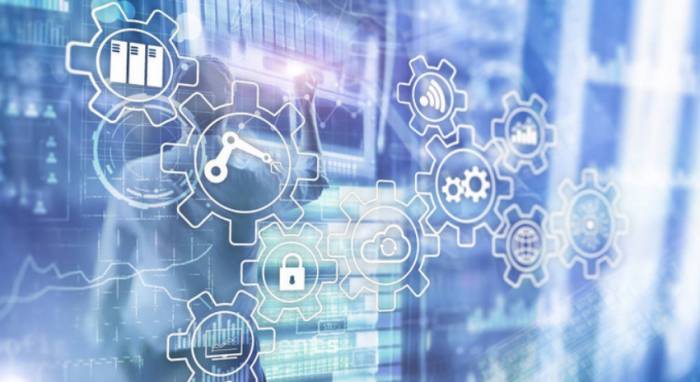
(2) Product Data Management Module. The input of part information generally includes basic dimensions, geometric topological information, material elements, and technical requirement information.
(3) Process Design Module. The process design module is the core module of the system, mainly completing process design based on case reasoning, including part feature coding, process case library search, extraction of similar process modifications, and editing functions. During the process design, the system can call the resource library at any time to query database information such as machine tools, jigs and fixtures, cutting tools, measuring tools, etc., facilitating the rapid acquisition of process design results that meet processing requirements and adapt to actual production in line with the existing resource situation of the enterprise.(4) Intelligent decision-making optimization in the process. Process decision-making includes generating process cards, calculating dimensions between processes, generating process diagrams; designing the content of work steps, determining cutting parameters, providing tool position files required for forming NC machining control commands; designing process parameters, and providing optimal process parameters based on intelligent algorithms.
(5) Process management module. Submitting well-prepared processes for review is an effective mechanism to ensure that the process information put into production is appropriate. Implementing online process review is one of the important parts of intelligent process design. Process review is usually divided into four steps: audit, standardization, co-signature, and approval, which are completed by different users.
(6) Process document management and output module. The ultimate goal of intelligent process design is to obtain process documents that can guide industrial production, so process document output is an indispensable part of intelligent process design. Since process documents mainly consist of process flow cards, process cards, and work step cards, selecting or customizing appropriate report output tools is the function of the process document output section.
`2. Requirements for Intelligent Process Design`
1) Analysis of intelligent process design requirements
Process design is an important link in product development, connecting product design with production manufacturing. The process documents it generates are important bases for guiding the production process and formulating production plans. Process design has a significant impact on the coordination of production, ensuring product quality, reducing production costs, improving product productivity, and shortening production time. Therefore, process design is an important task in manufacturing.
Process design requires the analysis and processing of a considerable amount of data, not only considering the structural shape, material, size, and production data of the designed parts but also understanding the manufacturing process, processing methods, processing equipment, manufacturing conditions, and processing costs. The relationships between these process data are intricate, and process personnel must comprehensively and meticulously analyze and process these process data when designing process plans. Traditionally, the design method of process plans has relied on the technical and experiential knowledge accumulated by process engineers in long-term production activities, conducted manually, with the quality of the process plan largely depending on the engineer's own level. There are widespread issues of repetition and diversity in process plan design. With the advent of the information age and the knowledge economy in manufacturing, the production of mechanical parts now dominates with a variety of small-batch production. The traditional process design methods are far from meeting the current industry development needs, which are specifically manifested as:(1) Relying on manual labor for process design is highly intensive, extremely inefficient, and highly subjective. According to relevant data, there is a 70% to 80% similarity in mechanical parts, and similar parts also have certain commonalities in their process routes. Effective actual work in process design may only account for about 8% of the total working time. Many enterprises spend a significant portion, approximately 55%, of their process preparation time on repetitive tasks such as calculating and copying process data. Process engineers need to spend a considerable amount of time on repetitive copying of process parameters, operation content, and process data aggregation during the process planning design, which increases their workload and leaves them with little time for creative work such as optimizing process plans. This prolongs the process design time and thus affects the entire product production cycle. Manual process design is difficult to optimize and standardize, which can easily lead to the waste of resources such as labor, equipment, and energy, increasing the manufacturing cost of products.
(2) The manufacturability of products is difficult to assess, and the means of process design and verification are outdated. Most manufacturing enterprises still use two-dimensional process cards with textual descriptions for process planning design. It is difficult to have a direct understanding of the existing process equipment and facilities during the process planning design. Process design cannot be simulated and analyzed, making it hard to evaluate existing process plans. Process information is stored on paper cards, which are not easy to store and are prone to loss, making it difficult to disseminate and reuse on a large scale.
(3) There is a lack of effective management of process data. Traditional process design uses paper archiving, making it difficult to reuse and manage existing process data effectively. How to extract typical processes from existing process documents and use process data resources more effectively, as well as to better inherit the company's long-accumulated process experience, are all important issues that need to be urgently addressed. The accumulation of knowledge and experience of process engineers is relatively slow, and there is a high turnover of technical personnel in enterprises. After they leave or retire, the knowledge and experience accumulated by engineers in process formulation work cannot be well preserved. New process engineers who join the company need to start learning process knowledge and experience from scratch, which to some extent causes a significant loss of the company's knowledge resources.
(4) The level of informatization is low, which is not conducive to the construction of informatization in the manufacturing industry. With the application of computer-aided software such as CAD, CAM, Computer-Aided Fixture Design (CAFD), Enterprise Resource Planning (ERP), Manufacturing Execution System (MES), and Computer-Aided Quality (CAQ), information between enterprises is transmitted through computer information technology. However, process design still uses outdated manual work, and process information is still stored on paper documents, which seriously hinders the exchange of information between various departments of the enterprise and affects the progress of enterprise informatization construction and work efficiency.
With the widespread application of CAPP, a large number of examples have shown that implementing intelligent process design can bring significant benefits. In a detailed survey of 22 large and small companies using generative process design systems, it was found that using such a system can reduce process planning work by 58%, labor by 10%, materials by 4%, and waste by 10%. Intelligent process design is gradually becoming a hot topic of research. The demand for the functionality of intelligent process design systems by enterprises is mainly concentrated in the following areas, as shown in Figure 2.Figure 2: Schematic Diagram of Enterprise Requirements for Intelligent Process Design System Functions
2) Analysis of Intelligent Process Design Model
Intelligent process design should further develop in the directions of tooling, engineering, integration, networking, knowledge-based, intelligent, flexible, and standardized, in order to lay a more solid and reliable foundation for enterprise information construction.
(1) Tooling and Engineering. The intelligent process design system emphasizes tooling and engineering to enhance the system's universality within enterprises. The overall system is decomposed into multiple relatively independent tools for development, with secondary development of the system oriented towards manufacturing and management environments, and integration of sub-systems with various specialized functions on a unified platform.
(2) Integration and Networking. The intelligent process design system achieves comprehensive integration of CAD/CAPP/CAM, with two-way information exchange and transmission of design data; effective integration with production planning and scheduling systems; and establishing an intrinsic connection with quality control systems. It realizes the comprehensive sharing of computational resources, storage resources, data resources, information resources, knowledge resources, and expert resources.
(3) Knowledge-based and Intelligent. Based on the development and application of composite intelligent systems, expert systems, artificial neural network technology, and fuzzy reasoning technology, the intelligent design system can perform self-learning and self-adaptation at various levels, further transforming process design data into advanced manufacturing knowledge, and further achieving intelligent process design.
(4) Flexibility and Standardization. Modern intelligent process design systems are based on interactive design, reflecting flexible design; with a process knowledge base at the core, they are oriented towards the flexible design and management of processes in the realization of products; with the product as the core, and the process route as the basis, they arrange the process of process work according to the process route, achieving standardization of the design process.
(5) Interactive and Progressive. Modern intelligent process design provides an interactive input and output interface based on process knowledge and judgment for process design personnel, while also providing a visual management platform for enterprise management, progressively advancing the development process of intelligent manufacturing.```
3. Evolution of Intelligent Process Design
The new generation of information technology is accelerating the development of intelligent manufacturing. The 3C electronics industry is facing challenges such as small batch and multi-variety production, rapid market changes, and mass customization, which necessitates the integration of intelligent manufacturing innovation. Intelligent manufacturing is a trend of the current era, and process design, as an important link in the manufacturing industry, directly connects product design with production. Achieving intelligent process design will greatly enhance the competitiveness of enterprises. The development of intelligent process design is based on the evolution of CAPP (Computer-Aided Process Planning), gradually integrating artificial intelligence algorithms primarily based on machine learning, combined with digital twin technology, to achieve the intelligent design of processes, reducing or even eliminating the impact of human factors, and improving the efficiency and quality of process design.
1) The development history of intelligent process design technology
The development of computer-aided process planning began in the late 1960s, as shown in Figure 3. In 1965, Niebel first proposed the concept of CAPP. CAPP originated from the application of group technology (GT) in process design and has now become a component of computer-aided manufacturing and computer-integrated manufacturing systems. With the development of mechanical manufacturing production technology and the current market's demand for multi-variety, small batch production, especially as CAD and CAM systems evolve towards integration, networking, and visualization, computer-aided process planning has increasingly gained attention. The earliest country to research CAPP was Norway, which officially launched the world's first CAPP system, AUTOPROS, in 1969, and officially launched the commercialized AUTOPROS system in 1973. A milestone in the history of CAPP development is the CAM-I'S Automated Process Planning system introduced by the international standard organization CAM-I based in the United States in 1976, named after its initials, the CAPP system.
Figure 3: The development history of intelligent process design technology
Research on CAPP systems in our country began in the late 1970s. The earliest developed CAPP systems in China were the TOJICAPP revision system from Tongji University and the CAOS generation system from Northwestern Polytechnical University. Subsequently, representative systems include the THCAPP system developed by Tsinghua University, the EXCAPP system developed by Beijing University of Aeronautics and Astronautics, the GNCAPP system developed by Northwestern Polytechnical University, and the NHCAPP system developed by Nanjing University of Aeronautics and Astronautics, all of which were completed in the early 1980s. To date, more than 50 CAPP systems have been published in domestic academic conferences and publications, but only a few have been officially applied in factories and enterprises, and there are still not many CAPP systems that have truly become commercialized.
```For many years, both domestic and international communities have conducted extensive discussions, research, and implementation of CAPP (Computer-Aided Process Planning) technology. The scope of CAPP systems has expanded from initially targeting a specific category of parts, such as rotational, box-like, and bracket components, to encompassing various types of components. The application has also broadened from a focus on individual parts to a comprehensive approach that considers the entire product.
Since its inception, the development of CAPP technology has been thriving globally. However, due to technological limitations and the customization and diversity of processes, the application of CAPP systems was previously quite narrow, suitable only for certain parts of a specific company, without a good general solution. It wasn't until the end of the 20th century, with the emergence of the tooling philosophy, that a batch of practical and commercial CAPP systems appeared, leading CAPP systems to a substantive application phase.
With the advancement of intelligent technologies, in addition to CAPP systems aimed at traditional process planning issues, intelligent process systems that focus on the expression of knowledge in specific process issues, decision optimization of processes, and three-dimensional simulation for design problems have also gradually come into view. However, despite these significant efforts, process design tasks are not yet fully automated and still rely on human experience and knowledge.
As new-generation information technology endows intelligent manufacturing with increasingly powerful cognitive and learning capabilities, it has greatly changed the boundary between humans and machines. An ideal intelligent process design system supports autonomous manufacturing through intelligent perception, simulation, understanding, prediction, optimization, and control strategies. It will be able to collect the experience and knowledge of technical experts and adapt and learn in real-time based on the data from the manufacturing process and work history. Embedding process planning into digital twin manufacturing cells not only enhances the connectivity between the upstream manufacturing cells and the design phase but also strengthens the connectivity with the downstream manufacturing phase. With the development of intelligent process design research, the goals and technical means of intelligence have evolved to place greater emphasis on efficiency and real-time performance compared to the past.
2) The Evolution of Intelligent Process Design Technology
Considering the development process of intelligent process design systems in our country, intelligent process design has undergone the following evolutionary process:(1)A specialized system for process design based on the concept of automation. From 1982 to the present, for a considerable period of time, the initial intelligent process design systems have been aimed at automating process design by replacing the labor of process engineers, that is, based on the concept of a specialized intelligent process design system. Emphasizing the automation of process decision-making, several types of variant, generative, and hybrid CAPP systems have been developed, which can automatically or semi-automatically compile process procedures. The practicality and versatility of this system are relatively poor, thus its application is greatly limited and it is difficult to achieve commercialization.
(2)A tool-type system for process design based on the concept of process management. Since 1995, intelligent process design tool-type systems based on the concept of process management have emerged. These systems have made breakthrough progress in practicality, versatility, and commercialization. The intelligent process design tool-type system, based on the analysis of customer needs, primarily aims to solve the transactional and managerial tasks in process design. It can use computer-aided methods to automatically complete tedious and repetitive tasks such as data retrieval, form filling, data calculation, and classification summarization in process design.
(3)Integrated CAPP systems and intelligent process systems based on data management. Since 1999, integrated CAPP systems and intelligent process design systems that focus on process data as the core have appeared. These systems are interactive computer application systems that integrate process design with information management, integrating retrieval, revision, and generative process decision-making hybrid technologies, as well as artificial intelligence technologies. They have achieved human-machine hybrid intelligence, integration of people, technology, and management, and have gradually realized the automation of process design.
(4)Intelligent process design systems based on real-time dynamic design. With the introduction of the digital twin concept in 2011, the mechanical processing process design has begun to introduce the concept of an as-built model (the machining status model of the workpiece). From the perspective of system construction, it has studied the three-dimensional process design technology for the digital twin environment and proposed a real-time process design method based on the as-built model. This provides a new approach for process design based on digital twins, enabling real-time decision-making and offline analysis optimization during the process design process, driving and leading the intelligent development of computer-aided process planning.
3)Development of intelligent process design systemsAs the demand for intelligent process design deepens, intelligent process systems have also come into the sights of researchers. Roughly starting from the late 20th century to the present, the development of intelligent process design systems has never stopped. It is the result of the application of artificial intelligence technology in the field of process design. A variety of intelligent process design systems have been developed to date.
(1) CAPP systems based on artificial neural networks. The most attractive features of artificial neural network (ANN) technology are its self-learning ability and fault tolerance. Through sample training, ANN can automatically acquire knowledge; through distributed storage and parallel processing of knowledge, ANN has strong fault tolerance, effectively compensating for the "narrow staircase effect" of expert systems. However, using ANN to simulate the process design decision-making process also has its fundamental flaws, such as the performance of ANN being largely limited by the chosen training samples, the quality of the samples directly determines the quality of the system performance; the knowledge expression and processing of ANN are implicit, users can only see the input and output, and cannot understand the intermediate reasoning process. Therefore, for process design, ANN can only simulate some simple decision-making activities with direct correspondence (cause and effect).
(2) CAPP systems based on case-based reasoning. Case-based reasoning CAPP technology is the application of analogy problem-solving methods in artificial intelligence technology in process design, and can also be seen as a further development of derivative CAPP technology. A case is a holistic description of process design knowledge, including not only the solution to the problem but also the conditions for solving the problem, which is highly consistent with the memory structure of human process design knowledge. Therefore, the acquisition of case knowledge is much easier than the acquisition of rules. Case-based reasoning is the reuse of past solutions, rather than re-deriving from scratch, and has high problem-solving efficiency and practicality. CAPP technology based on case-based reasoning has been studied by many scholars.
(3) Knowledge-based intelligent process systems. Various knowledge expression and reasoning techniques in knowledge engineering have greatly enriched and expanded the knowledge expression and processing capabilities of traditional generative process systems, enabling expert systems to handle some more complex process decision-making problems, and some expert systems have approached practicality. However, as research and application continue to deepen, some inherent flaws in the traditional knowledge representation and reasoning techniques of expert systems gradually emerge: such as the bottleneck of knowledge acquisition, the "narrow staircase effect" of system performance, and the limitations in dealing with fuzzy, non-monotonic, and common-sense problems.
Many early intelligent studies were based on expert systems, using computational module plug-in formats in the process decision-making module as expert system tools, combining rule-based knowledge representation languages with process languages, and then building a knowledge base through the use of production rules, and adopting deductive reasoning reasoning machines, theoretically achieving a series of process decisions. In fact, this only provided ideas for the intelligent research of early process systems. Based on the hardware and software conditions at the time, it did not involve artificial intelligence algorithms, nor did it build practical intelligent systems.
(4) Distributed artificial intelligence process design systems. Most human activities involve social groups, and solving large and complex problems requires the collaboration of multiple professionals or organizations. With the development of computer networks, computer communication, and parallel programming design technology, such technologies have gradually become a new research hotspot. At the beginning of the 21st century, process design represented by artificial intelligence technology has increasingly attracted the attention of researchers and may become an important breakthrough in the development of the next generation of intelligent process design system software. Building a distributed intelligent process design system that includes CAPP systems and intelligent process systems can overcome the weaknesses of the original centralized knowledge systems, greatly improve the performance of the system, including problem-solving ability, solution efficiency, and reduce the complexity of the system.(5) The application of other intelligent technologies and algorithms. Fuzzy reasoning technology, evolutionary computation technology, and particle swarm optimization have also been applied to varying degrees in process design. At the same time, the application of intelligent algorithms such as genetic algorithms and ant colony algorithms has played an active role in broadening the information processing capabilities of intelligent process design systems and improving system performance. Product digital twin technology, by continuously accumulating relevant data and knowledge throughout the entire lifecycle of product design, manufacturing, and inspection, achieves a virtual-physical mapping between cyberspace and the physical world, providing an effective approach for the development of computer-aided process planning technology and the resolution of bottleneck issues.
Comment