Application of APS in core automotive components
2024-08-26 / tech
The automotive core components industry is a broad and complex field, encompassing multiple key systems and parts that together form the overall structure and functionality of a vehicle.
Here are the main categories of the automotive core components industry:
1. Powertrain components, such as: engines, transmissions, fuel systems, exhaust systems, electric motors (new energy), power sources, electronic controls (new energy)
2. Chassis system components, such as: suspension systems, braking systems, tires, steering systems
3. Body system components, such as: body frames, interior parts, exterior parts
4. Electrical and electronic system components, such as: battery and charging systems, lighting systems, control systems
01Key Characteristics of Automobile Core Component Manufacturing
1. High Precision Requirements
As the core components of automobiles, there is a very high demand for precision, including the dimensions of the parts, the fit accuracy, and the selection of materials. It is necessary to strictly control various parameters during the production process to ensure product quality.
Advertisement
2. Complex Manufacturing Processes
The production of large core components involves a variety of complex technologies and processes, such as casting, forging, heat treatment, mechanical processing, assembly, etc. These technologies and processes require highly specialized and skilled workers to operate.
3. High Level of Automation
With the development of technology, the production of the automotive industry and its components has gradually achieved automation and intelligence. For example, the processing and assembly of components are realized through automated equipment such as numerical control machines and robots, which improves production efficiency and product quality.4. Multi-variety, Small-batch Production
Due to the core components of automobiles requiring customization based on different vehicle models and configurations to meet the needs of various customers and different year models, production exhibits the characteristics of multi-variety and small-batch. This demands that companies have flexible production organization and scheduling capabilities to satisfy the demands of different customers.
5. Strict Supply Chain Management
The production of automotive core components involves multiple suppliers and the procurement of parts, necessitating the establishment of a comprehensive supply chain management system to ensure the quality of components and the stability of supply. Additionally, it is essential to establish close cooperative relationships with suppliers to jointly address market changes.
6. Market Fluctuations
The uncertainty of customer demand, especially changes in demand from vehicle manufacturers, can make it difficult for component suppliers to predict order volumes, thereby affecting the stability of production planning.Automotive Core Components Planning Model and Characteristics
1. Market Demand Driven
Primarily driven by market demand, companies formulate production plans based on market research and forecasts, in conjunction with the development trends of the automotive industry.
2. Lean Production and Inventory Control
Automotive core components tend to adopt a lean production model, which optimizes production processes, reduces waste, and increases production efficiency to meet the rapidly changing market demands.
Under the lean production model, companies closely monitor market demand and production capacity to achieve minimal inventory and improve capital turnover rates.3. Multi-process and Multi-workshop Production Collaboration
The production of automotive core components often involves multiple processes with different technologies, which are completed by different workshops (factories) responsible for their respective production tasks. The collaboration between different processes in terms of supply and demand is particularly important, as the production characteristics and considerations for different processes are entirely distinct. For instance, during final assembly, factors such as the supply of semi-finished goods, procurement of long-cycle materials, personnel capacity, and balanced production on the assembly line must be considered. In machining workshops, the coordinated production of different components, the allocation of capacity between in-house and outsourced production lines, the usage cycle of cutting tools, and maintenance rules must be taken into account. In heat treatment workshops, the rational allocation of furnaces is crucial, and in casting workshops, the usage and maintenance cycles of jigs, tools, and molds are essential.
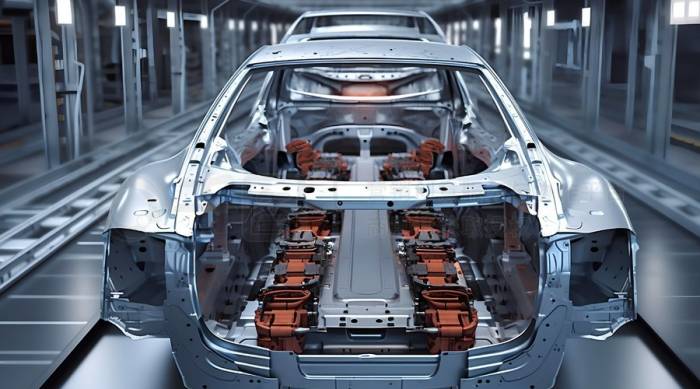
4. Flexibility and Rapid Response
Automotive core components are typically produced in a flexible manufacturing mode, requiring quick adjustments to production arrangements based on market demands and capacity changes. Enterprises must respond swiftly to market changes to meet the diverse needs of customers. This demands that production lines have the capability to switch rapidly between different products, adapt flexibly to market changes, and enhance production efficiency.
5. Traceability in Production
The production of automotive core components is subject to legal and regulatory requirements that each component must have a unique identifier, such as a barcode or QR code, for easy recognition and tracking. This places higher demands on production scheduling, which must be able to trace back to each process, each step of the actual production time, the batch of materials used, and the inspection status through the production plan.Challenges Faced by Traditional Production Planning Models in This Industry
1. Inaccurate Demand Forecasting
Due to factors such as significant market demand fluctuations and high customization requirements, it is difficult for companies to accurately predict future needs, leading to difficulties in executing production plans. Especially with the rise of new domestic automotive forces, the impact on traditional fuel vehicles is considerable, and production capacity needs to be more inclined towards new energy products.
2. Slow Response Speed
The traditional production planning model is slow to respond to changes in market demand, making it difficult to adjust production plans in a timely manner. This is particularly true with the rise of electric vehicles (EVs), autonomous driving cars, and intelligent connected vehicles, where the technical requirements for automotive components are rapidly changing. Traditional production plans may struggle to keep up with the pace of technological iteration.
3. Low Efficiency
Issues such as frequent model changes on production lines and poor material management lead to low production efficiency and high costs. This is because during the planning and scheduling process, there are many different conditions and constraints to consider, such as overseas procurement of material inventory, personnel, resource attendance, tooling, mold life, and maintenance strategies, as well as supporting production, both internal and external, and inventory control.4. Inventory Management and Cost Control
Traditional production planning models often lead to high inventory levels, with stockpiling occupying a significant amount of capital and increasing inventory costs. At the same time, due to uncertainties in the production process, companies often need to meet customer demands through overtime work, delayed deliveries, and other means, which also increases production costs.
5. Disconnection between Planning and Execution
Traditional production planning models often have inconsistencies and mismatches between planning and execution. Material procurement plans are decoupled from actual production, and the procurement cannot keep up with the production schedule, leading to production delays. There is a lack of a more precise, realistic, and optimized production planning tool, which prevents companies from accurately answering how many orders can be completed and where the execution layer has issues that prevent plans from being completed on time.
6. Supply Chain Complexity
The supply chain for automotive parts is long and complex, potentially involving suppliers from all over the world. Traditional planning models are slow to respond to supply chain disruptions, logistics delays, or supplier issues, leading to difficulties in scheduling production, analyzing planning problems, confirming exceptions, and achieving actual production, among many other challenges.04
Application of APS Systems in the Automotive Parts Industry
1. Demand Forecasting and Inventory Management
APS systems can integrate historical sales data, market trends, and seasonal variations to provide more accurate demand forecasts. This helps component manufacturers to plan their inventory rationally, avoiding both overstock and stockouts, and provides strong support for production planning. As a result, inventory management standards may be established along different dimensions, such as setting minimum inventory, benchmark inventory, and maximum inventory by machine type, and defining the inventory storage capacity at the production line or workshop level based on the location of inventory storage. During the planning and scheduling process, demand and inventory strategies are combined to refine production scheduling.
2. Rapid Response to Market Changes
APS systems are capable of adjusting production plans in real-time, simulating the impact of demand changes on plans under various conditions, and responding quickly to market changes to ensure that the execution of production plans matches market demands. When there is a change in demand, the system can quickly access the latest data through interfaces. The APS then automatically updates the plan based on preset scheduling logic (which is configurable based on expert rules and can be quickly adjusted according to changes in business needs without the need for code modification or re-development), comparing multi-dimensional changes such as demand, plans, and inventory.
3. Production Planning and Scheduling
(The original text ends abruptly, and the translation is incomplete. The rest of the section on production planning and scheduling is not provided.)The APS system can automatically calculate and optimize production scheduling based on the actual situation of resources such as equipment, materials, and personnel, thereby improving production efficiency. During the production planning and scheduling process, it takes into account resource constraints, priorities, and delivery dates to generate a feasible production schedule. This helps to reduce production cycle times and increase the utilization rate of production lines. It can intelligently allocate production resources, such as machines, tools, molds, labor, and raw materials, ensuring the best use of resources, reducing waste, and idle time.
4. Order Processing and Customized Production
In response to the personalized needs of the automotive industry, the APS system supports a mixed mode of make-to-order (MTO) and make-to-stock (MTS) production, flexibly handling various types of orders, including mass and small batch customization. It can achieve functions such as: machine inventory control (minimum and maximum inventory), overall inventory management capacity, number of switches, production line machine constraints, kit production, tooling and fixture lifecycle management, automatic planning of production capacity, and consideration of overtime for different business needs.
5. Collaborative Supply Chain Management
The APS system can establish close collaborative relationships with the company's suppliers, logistics companies, etc., and can connect the production planning and scheduling of different processes, achieving real-time linkage and transparent management and optimization of the supply chain. The APS system promotes collaboration between upstream and downstream of the supply chain, such as real-time information exchange with vehicle manufacturers, allowing for dynamic adjustment of plans to respond to changes in vehicle manufacturers' needs, ensuring the timely delivery of parts.
6. Exception Handling and Contingency Planning
The system can quickly identify exceptions in the production process, such as equipment failures or material shortages, and provide alternative solutions or contingency plans to reduce the risk of production interruptions. It supports rapid adjustment and simulation of plans under exceptional circumstances, reducing the impact of exceptions on actual production.05
Value of APS Application
1. Enhancing Production Efficiency and Flexibility
APS systems, through advanced algorithms and flexible model configurations, can automatically optimize production planning and scheduling, taking into account resource constraints, priorities, delivery times, and production costs. This enables factories to maximize production efficiency and resource utilization while meeting customer orders, thereby reducing production costs.
2. Improving Customer Satisfaction
APS systems can quickly respond to market changes and customer demands, ensuring timely product delivery. By optimizing production processes and resource allocation, they reduce production cycles and accelerate the transformation of products from raw materials to finished goods, thus shortening the delivery time to customers and enhancing customer satisfaction.3. Optimize Inventory Management
The APS system can accurately predict market demand and, while ensuring delivery, can reasonably arrange production plans based on factors such as minimum inventory per model, benchmark inventory, maximum inventory, inventory storage capacity, and material stock levels. This helps to reduce inventory backlog and waste.
4. Improve Resource Utilization
The APS system can intelligently schedule production equipment and human resources to ensure that the right resources are available at the right time, reducing waiting time and increasing the overall efficiency of resource use, thus minimizing resource waste.
5. Enhance Supply Chain Collaboration
The APS system can be integrated with other supply chain management systems (such as ERP, SCM, MES, SRM, etc.) to achieve real-time information sharing and collaboration. This ensures synchronized operations between upstream and downstream of the supply chain, improving the response speed and efficiency of the entire chain.
6. Cost Control and Analysis
The APS system can effectively control and analyze costs by monitoring and managing various cost factors throughout the production process. This allows for the identification of areas where costs can be reduced and for the implementation of strategies to optimize cost efficiency.The APS system can automatically optimize production plans based on the manufacturing costs of products (specific to a particular production line or machine), selecting the resource arrangement with the lowest production cost while meeting customer demands. It can also automatically perform statistical analysis of the cost areas for purchased and self-produced items, providing decision-making support for the leadership in procurement strategies.
Comment