A panoramic view of servo motors: How to open the era of precision control?
2024-08-21 / tech
In May of this year, the official account of Tesla Optimus posted a video on social media platform X. In the video, Optimus is skillfully sorting battery cells on the production line at the Tesla factory, with smooth movements thanks to its built-in high-performance servo motors.
In addition to the currently popular humanoid robots, servo motors are widely used in fields requiring high-precision motion control and positioning, such as CNC machines and industrial robots. For instance, servo motors are not only used to drive and control the main spindle, feed axis, and automatic tool change system of CNC machines, enabling them to change tools accurately and smoothly move according to numerical control codes, following preset paths to skillfully perform operations like cutting, drilling, and milling; they can also be used to drive and control the joints and end-effectors of industrial robots, allowing them to accurately and repeatedly complete tasks such as welding, gluing, painting, and assembly along specified paths; they can also drive and control the conveyor belts and sorting units of automated production lines, ensuring materials are precisely transferred between different processes, which is truly astonishing given the powerful motion control capabilities of servo motors that drive various shafts. It can be said that in all scenarios involving motion control, servo motors play an indispensable role, and the application of servo motors signifies the beginning of an era of precision control!
The development history of servo motors:
Servo, derived from the Greek word σέρβο, originally means "slave". The term was first used to describe a system capable of automatically executing commands, similar to the concept of a slave obeying the master's orders.
A servo motor can be understood as a motor that absolutely obeys the command of control signals.The advent of the world's first direct current (DC) servo motor can be traced back to the 1950s. In 1958, Fukuda Mitsuyuki, a technical engineer at Yaskawa Electric, invented the world's first direct current (DC) servo motor—the Minertia motor. This motor was entirely controlled by current and voltage, which increased its response speed to 100 times that of ordinary motors at the time, greatly enhancing the production efficiency of enterprises.
Advertisement
During the 1950s and 1960s, the technology of direct current (DC) servo motors continued to develop and improve in practicality, and they began to be used in industrial robots to replace hydraulic and pneumatic mechanisms that had issues with precision, stability, and piping.
By the 1980s, alternating current (AC) servo motors emerged. Due to their higher practicality, they are now almost used in equipment across all industrial fields. Notably, the Indramat division of the German MANNESMANN Rexroth company officially launched the MAC permanent magnet AC servo motor and driver at the 1978 Hanover Trade Fair, marking the entry of a new generation of AC servo technology into the practical application phase.
In the mid-to-late 1980s, various companies had complete product lines, and the entire market gradually shifted towards AC servo systems. High-performance electric servo systems mostly use permanent magnet synchronous AC servo motors, with typical manufacturers including German Siemens, American科尔摩根 (Kollmorgen), Japanese Panasonic, and Yaskawa, among others.
In the 1990s, with the application of microprocessors and new digital signal processors (DSPs), servo systems emerged where the control part could be entirely executed by software. This allowed the functionality of servo systems to be enhanced or modified by updating the software without changing the hardware. For instance, in the AC servo system of permanent magnet synchronous motors (PMSM), the TMS320LF2407 chip was used as the control core to achieve speed and position control of PMSM AC servo motors, demonstrating that DSP-controlled AC servo systems have the advantages of a wide speed range, accurate rotor positioning, fast response, high intelligence level, and good dynamic and static performance.Entering the 21st century, with the rapid development of digitalization, networking, and intelligent technologies, servo motor systems have also ushered in a new round of technological innovation. Digital servo drivers are equipped with high-performance processors that can implement complex control algorithms and rapid data processing to enhance system performance.
Servo Motor Working Principle
Returning to the beginning of the article, when Optimus receives an instruction to pick up a certain battery cell and move it to a specified location and then put it down, in order to complete this action, the instruction is transmitted to the servo system. It uses a closed-loop feedback control circuit to adjust the rotation speed and torque of the corresponding servo motor with astonishing speed and accuracy, ensuring that the corresponding joint performs the action smoothly and precisely. Next, this article will reveal how the servo motor works under the control of the servo system.
- Upon receiving the target instruction, the controller first transmits a control signal to the driver;
- The driver then converts the control signal into a drive signal and transmits it to the actuator;
- After receiving the drive signal, the actuator begins mechanical motion and outputs motion information to the feedback device. At the same time, the feedback device also starts to provide real-time feedback of the actuator's motion information to the driver;
- The driver compares the feedback signal with the control signal and continues to output an adjusted drive signal to the actuator, which promptly adjusts its motion. This cycle continues until the actuator outputs the mechanical motion required by the target instruction.Thus, the servo system has achieved the purpose of controlling motion according to target commands.
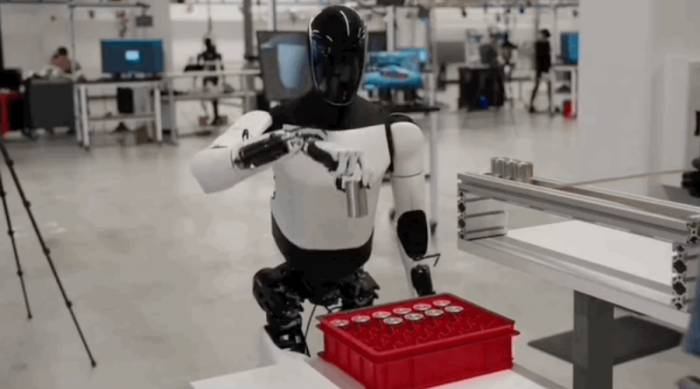
In general, a servo system is a closed-loop feedback control system that can precisely control the position, speed, acceleration, or other parameters of an actuator, and a servo motor is an actuator specifically designed for precise control of mechanical motion.
After receiving the drive signal through the cable, the rotor of the servo motor drives the shaft to rotate, completing the output of torque, while the encoder feeds back real-time motion information such as the rotation angle, number of turns, speed, and direction of the servo motor to the driver.
An important characteristic of the servo motor is its ability to respond quickly and accurately to changes in the drive signal and to maintain high-precision position control during motion. From the perspective of motion control, it is the servo system that endows the servo motor with the ability to control motion, and the precision of its motion control depends on its own structure, the resolution of the encoder, and the overall performance of the servo system in which it is located.
The most significant structural difference between a servo motor and other motors is the built-in encoder, which forms the basis of the closed-loop feedback control system. Servo motors generally adopt three types of closed-loop control: current (torque), speed, and position, to enhance their precision in motion control. In addition, thanks to the application of digital signal processing technology, high-resolution encoders, and advanced control algorithms, the precision control capabilities of servo motors are far superior to those of other motors.Servo Motors vs. Other Motors
Specifically, traction motors are characterized by their ability to generate high torque and power under heavy loads, but their motion control capabilities are far inferior to those of servo motors. Variable frequency motors emphasize a wide power range and strong speed variation capabilities, but their motion control capabilities also fall short compared to servo motors. Stepper motors achieve high positional accuracy through pulse signals, but they are susceptible to load changes, which can lead to missed steps, and they lack a closed-loop feedback mechanism for self-correction. Although stepper motors are also commonly used in motion control applications, the control precision of a servo motor equipped with a 17-bit encoder is approximately 600 times that of a stepper motor. The control precision of servo motors far exceeds that of stepper motors.
It is worth noting that other motors can also achieve closed-loop control in conjunction with external sensors and controllers, but the "inherent" closed-loop control structure of servo motors allows them to surpass the control precision of traction, variable frequency, and stepper motors, among others. Secondly, the control objectives differ: the control purpose of traction motors is for power management, efficiency optimization, and overload protection; the control purpose of variable frequency motors is to adjust speed; the control purpose of stepper motors is to address the issue of missed steps, while the control purpose of servo motors is to comprehensively control the position, speed, and torque of the motion they output.
In summary, servo motors meet the advanced application requirements for comprehensive control of precision, position, speed, and torque due to their attributes of accurate positioning and rapid response.Classification and Application of Servo Motors
Servo motors can be found in a variety of applications, from industrial robots to general-purpose robots, from ship steering gears to automated production lines. However, the requirements for servo motors in different application scenarios also vary. Servo motors can be broadly categorized into two main types based on the type of motion they output: rotary servo motors and linear servo motors. They can also be divided into two main categories based on the power supply method: direct current (DC) servo motors and alternating current (AC) servo motors. It is important to note that when referring to DC/AC servo motors in the market, it usually pertains to rotary DC/AC servo motors.
This article will primarily introduce the three commonly used types of servo motors in the market: rotary DC servo motors, rotary AC servo motors, and linear servo motors. Each type of servo motor has its own characteristics and advantages, and the choice should be made based on actual needs and budget considerations.
1. Rotary DC Servo Motors
Rotary DC servo motors are divided into brushed and brushless types. Brushed rotary DC servo motors have a physical commutator, which is cost-effective and simple to control, making them suitable for the civilian market that is sensitive to costs. However, the physical commutator requires frequent maintenance.Brushless direct current (BLDC) servo motors are known for their high performance, achieved through electronic commutation for current switching. They boast advantages such as compact size, fast response, energy efficiency, and long lifespan, but they come with relatively higher costs and more complex control systems, often used in industrial environments.
For instance, in the field of industrial robotics, the end-effectors require motors that can provide high torque or high speed, be compact, lightweight, and precisely controlled. In this domain, BLDC servo motors are the go-to choice. Whether it's the end-effector (claw) of a welding robot, the lifting column and gripper of an autonomous picking robot, or the drive for the directional wheels of an Automated Guided Vehicle (AGV), BLDC servo motors are typically employed.
In the semiconductor industry, the placement of surface-mount components onto the PCB pads by the pick-and-place head of a placement machine is achieved through BLDC servo motors. Beyond placement machines, other semiconductor automation equipment movements, such as wafer handling, visual inspection, SMT material storage, and wave soldering, are all realized using BLDC servo motors. In similar motion-related fields, BLDC servo motors can fully demonstrate their capabilities.
In the medical industry, the application of BLDC servo motors is primarily reflected in the automation of precision instruments. For example, in parallel bioreactors, BLDC servo motors are mainly responsible for precisely controlling key parameters such as stirring inside the reactor, bubble introduction (oxygen supply), pH adjustment, and temperature control, ensuring that the biological cultivation environment in each reaction unit is stable and reproducible.
In summary, with their advanced technical characteristics, BLDC servo motors have become a core technological component in modern precision manufacturing and automated services.2. Rotary AC Servo Motors
The primary control difference between rotary AC and rotary DC servo motors lies in the speed control mechanism. The speed of a rotary DC servo motor varies directly with the supply voltage, whereas the speed regulation of a rotary AC servo motor depends on the current frequency and the number of poles. This allows rotary AC servo motors to handle higher loads.
Rotary AC servo motors are divided into synchronous and asynchronous types. In a synchronous motor, the rotor rotates at the same speed as the stator's magnetic field, while in an asynchronous motor (induction motor), the rotor's speed is slightly less than that of the stator's magnetic field. Therefore, synchronous motors are more widely used due to their higher control precision.
In recent years, thanks to the development of high-performance permanent magnets, permanent magnet synchronous rotary AC servo motors have become the preferred choice in the field of industrial control. The advantages of permanent magnet synchronous rotary AC servo motors can be summarized as "three highs": high performance, high precision, and high response speed. Within their rated power range, they can achieve constant torque, low inertia, and low-noise operation. They are suitable for dust-free and explosive environments due to their brushless wear and maintenance-free characteristics, but they must comply with relevant safety regulations and standards. When selecting and using permanent magnet synchronous rotary AC servo motors, the specific requirements of the environment and the motor's explosion-proof rating must also be considered.
In the CNC machine tool industry, permanent magnet synchronous rotary AC servo motors are used to control the rotation speed and direction of the spindle; drive the tool change mechanism, precisely controlling the loading and unloading actions of the tools; and precisely control the positional movement of the tool or worktable, ensuring the accuracy of each step in the machining process.
In the medical industry, permanent magnet synchronous rotary AC servo motors are used to control the movement of internal components of equipment such as CT scanners, X-ray machines, and magnetic resonance imaging (MRI) devices, such as the rotation of the platform and the movement of the scanning arm, to ensure stability and accuracy during image acquisition. They are used in ventilators and anesthetic machines to control gas flow and pressure, maintaining the stability of the patient's respiratory cycle. In ophthalmic laser surgery equipment, permanent magnet synchronous rotary AC servo motors can control the precise movement of the laser beam, ensuring accurate positioning and treatment of the surgical site.In the field of industrial robotics, permanent magnet synchronous rotating AC servo motors are installed at the "joints" of robots, driving the extension, rotation, and translation of the robot arms, enabling the robot arms or end-effectors to reach predetermined positions. This is crucial for high-precision assembly, painting, gluing, and other tasks. Coupled with advanced control algorithms, these motors enable robots to move precisely along preset complex trajectories, meeting the demands of precision machining and assembly.
In addition to playing an irreplaceable role in the three key areas mentioned above, the applications of permanent magnet synchronous rotating AC servo motors are countless in other industries.
The wide range of application scenarios for permanent magnet synchronous rotating AC servo motors highlights their indispensable position in the contemporary field of industrial control.
3. Linear Servo Motors
In recent years, with increasing demands for equipment precision and speed, the application of various linear servo motors has been promoted, gradually demonstrating their value in their respective fields.Linear servo motors operate by linear actuation, and their structure can be understood as unfolding the internal structure of a rotary servo motor along a straight line and swapping the positions of the stator and the rotor, thereby achieving the purpose of directly driving the load to perform linear motion. They are equipped with a linear encoder that measures the rotor position by reading grating lines or magnetic strips engraved on a glass or metal scale.
Compared to ball screw drives, linear drives have the advantages of high energy conversion efficiency, high speed, high precision, high acceleration efficiency, simple construction, and easy use due to the absence of mechanical structures such as ball screws.
The applications of linear servo motors overlap with those of other servo motors. In the semiconductor industry, they are used in wafer handling and photolithography equipment to ensure precise positioning operations of wafers.
In the logistics industry, automatic sorting systems adopt linear servo motors to achieve fast and accurate sorting of goods; and in large material handling systems such as airport baggage handling systems, the application of linear servo motors also ensures the rapid and accurate transmission of luggage.
In the automated welding production lines of the automotive manufacturing industry, linear servo motors are used to precisely control the movement of the welding gun, ensuring the accurate alignment of the welding points.In the positioning of hard disk drive read/write heads and the micro-motion control of semiconductor chip testing equipment, linear servo motors play a crucial role due to their rapid response and high precision characteristics.
In the food/pharmaceutical packaging industry, filling and sealing equipment widely utilize linear servo motors for their wear-free, high flexibility, and low friction characteristics. They enable fast positioning and precise control of the filling nozzle, ensuring the efficiency and hygiene of the production line.
Development Trends of Servo Motors
To meet the increasingly complex and variable production demands, future manufacturing will rely more on high-performance, energy-saving, and versatile servo system solutions. As the core component of the servo system, the development trend of servo motors is closely linked to this, specifically manifested in the following three aspects:
1. High EfficiencyEfficiency has always been a primary concern in the development of servo motors. As the manufacturing industry transitions towards automation and intelligence, the performance requirements for servo motors are increasingly demanding, including the enhancement of efficiency. Moreover, the global awareness of environmental protection has prompted companies to seek more energy-saving solutions to reduce energy consumption and carbon emissions. From the perspective of corporate cost and benefit, efficient servo motors can not only reduce energy consumption but also lower long-term operational costs, bringing economic benefits to enterprises. These are the main factors driving the continuous strengthening of the demand for efficient servo motors.
International manufacturers typically update their servo products every five years, with product life cycles becoming shorter and changes occurring more rapidly. Summarizing the technological paths of various servo motor manufacturers, it is clear that the new generation of products in the same series has a certain improvement in efficiency compared to the previous generation, and this trend continues.
Efficiency is reflected not only in the high efficiency of the servo motor itself, such as the improvement of permanent magnet materials and the optimization of servo motor structure, but also in the high efficiency of the drive system, such as the optimization of inverter drive circuits, the optimization of acceleration and deceleration movements, the improvement of regenerative braking and energy feedback mechanisms, and excellent cooling strategies and methods.
Efficient servo motors are not only an inevitable trend of technological development but also a necessary means to address current industrial challenges and societal demands. As technology advances and market demands change, efficient servo motors will continue to be a key area of research and development to meet people's expectations for an environmentally friendly, low-energy, and sustainable society.
2. Integration and All-in-One
In the fields of industrial automation, CNC machines, and robotics, the market's demand for high precision, rapid response, space saving, cost reduction, simplified installation, and commissioning is increasing. The trend towards the integration and all-in-one design of servo motors has become a consensus in the industry. The integration of servo motors refers to the high integration of various functional modules of the servo motor into a compact system, giving it higher performance, lower energy consumption, and easier installation and maintenance characteristics. For example, companies such as Yaskawa, Siemens, Delta, and Inovance Technology have each launched servo motors with varying degrees of integration. This trend is reflected in the following aspects:Integrated Drives, which integrate the servo drive directly into the motor itself. This all-in-one design reduces the complexity of system wiring and space occupation, enhances electromagnetic compatibility, and improves system reliability.
Integrated Communication Modules, to achieve seamless communication with the upper control system, modern servo motors integrate various communication interfaces and protocols, such as EtherCAT, PROFINET, Ethernet/IP, etc. This integration makes it easier for servo motors to connect to industrial networks, enabling remote monitoring and distributed control.
Integrated Sensors, in addition to position and speed feedback, integrated servo motors may also include other types of sensors, such as temperature sensors, vibration sensors, etc. These sensors can provide more operational data, helping to achieve condition monitoring and preventive maintenance.
The trend towards integration and all-in-one design makes the structure of servo motors more compact and lighter in weight. This is of great significance for some space-limited applications, such as robots, drones, etc. The compact design not only saves space but also enhances the dynamic performance of the system. The integration of the motor, drive, and control tightly integrates the three from design, manufacturing to operation, and maintenance.
3. Polarization
In the future, servo motors will develop in two directions, mainly in terms of size and frequency. With the rapid progress of electronic technology and material science, servo motors are continuously moving towards miniaturization and lightweight. This trend of miniaturization is mainly reflected in the following aspects: First, the motor housing size is continuously reduced, thereby reducing the installation space requirements of the servo system. This is beneficial for the application of the servo system in confined spaces. Second, the use of new magnetic materials and winding designs makes the motor more efficient and high-power-density, providing a technical foundation for miniaturization.Corresponding to the trend of miniaturization, large-scale development is also another direction for the evolution of servo motors. For large industrial equipment and high-power devices, there is a need for servo motors with greater power. These large servo motors can provide more robust driving force. Typically, large servo motors adopt structures such as three-phase asynchronous motors or permanent magnet synchronous motors, capable of delivering higher torque and power. Large servo systems are usually equipped with more powerful electronic control systems, enabling more precise control of position and speed. Their applications include fields such as metallurgy, wind power, and large machine tools.
In summary, the development of servo motors reflects a trend of both miniaturization and large-scale development. Miniaturization is advantageous for broader applications, while large-scale development meets the needs of high-power drive. Future servo motor technology will continue to innovate and optimize in these two directions.
Current Status of the Servo Motor Market
In recent years, with the gradual increase in performance requirements for control motors in industries such as mechanical manufacturing and industrial robotics, the market size for servo motors has also grown. Globally, according to data published by Grand View Research, the global servo motor market size was 46.5 billion RMB in 2023, and it is expected that the global servo motor market size will continue to grow. It is anticipated that by 2026, the global servo motor market size could reach 55.9 billion RMB, with a compound annual growth rate (CAGR) of 6.32% over the next few years.
The continuous expansion of the global servo motor market is attributed to the combined effect of several key factors: First, the acceleration of industrialization in emerging economies, especially the increasing investment in automated production lines in countries like China and India, provides a vast market space for the application of servo motors. Second, the demand for intelligent upgrades to existing production lines in mature markets such as North America and Europe also drives the incremental market for servo motors.In the Chinese market, driven by the wave of intelligent manufacturing, the manufacturing industry is increasingly adopting advanced automation solutions, which also drives the growing demand for servo motors in the Chinese market. According to data released by QYResearch, the market size of China's servo motor market increased from 13.3 billion yuan in 2018 to 18.1 billion yuan in 2022, and the market size of China's servo motor market in 2023 is 19.5 billion yuan; it is expected that the market size will reach 22.5 billion yuan in 2026, with a compound annual growth rate (CAGR) of 4.88% over the next few years.
Figure 7: Market Size and Forecast of Servo Motor Market from 2018 to 2026 (Data source: Grand View Research, QYResearch, compiled by e-works)
In the Chinese servo motor market, the AC servo motor market accounts for the main share, with a market share of 65%, while the DC servo motor accounts for 35%. The largest application field for servo motors in China is machine tools (especially CNC machine tools), with a share of 20.4%, followed by electronics manufacturing equipment, packaging machinery, textile machinery, plastic machinery, industrial robots, and other industries, with respective shares of 16.5%, 12.6%, 12.1%, 9.6%, and 6.20%.
From the perspective of market competition, due to the first-mover advantage of international manufacturers in the development of servo motors, the main share of the servo motor market is currently occupied by international manufacturers. At present, internationally renowned servo motor manufacturers include Yaskawa Electric, Mitsubishi Electric, FANUC, Siemens, Panasonic, etc. These international manufacturers have advanced technology, a wide range of products, strong brand influence, and a global sales network, thus occupying a dominant position in the global servo motor market.
Although domestic local manufacturers started relatively late in the development of servo motors, with continuous efforts in research and development and application promotion in recent years, they are gradually enhancing their competitiveness in the servo motor market and narrowing the gap with international brands. Moreover, after lying low in the mid-to-low-end market for many years, domestic local servo motor manufacturers have begun to enter the high-end market. At present, well-known domestic servo motor manufacturers mainly include Inovance Technology, Estun, Hechuan Technology, Xinjie Electric, Wolong Electric Drive, Lelans Intelligent, Megmeet, Haozhi Electric, Bukel Automation, Midea Industrial Technology, and Taiwan manufacturers such as Delta and TECO Electric & Machinery.Internationally Renowned Servo Motor Manufacturers (listed in no particular order)
01
Yaskawa Electric
Official Website:
Established in Japan in 1915, Yaskawa Electric initially focused on the production of electric motors and later expanded into a wide range of industrial automation products and services, including servo motors, frequency converters, and industrial robot technology. Yaskawa Electric is a significant player in the servo motor market, offering high-precision, high-performance servo systems, including servo motors and servo drivers. The company mainly has three major series of AC servo motors: Sigma-X, Sigma-V, and Sigma-7. The Sigma-X series, as an iteration of the Sigma-7 series, enhances motion performance while supporting the flexible use of data sensing functions. The Sigma-V series breaks the common sense of "it cannot run smoothly without adjustment," achieving plug-and-play, which can shorten installation time and fully utilize the mechanical performance of the servo motor. Its flagship Sigma-7 series of AC servo motors is known for its stability, speed, and cost-effectiveness, capable of stable operation over a wider range of temperatures and humidity, making it suitable for various applications such as liquid crystal panel processing, precision measurement equipment, medical devices, packaging machinery, and industrial robots.
02
Mitsubishi Electric
Official Website: Electric was founded in 1921, headquartered in Japan, and is a leading global supplier of industrial automation products, with a factory automation (FA) product range that spans all levels of manufacturing and covers the entire manufacturing chain. As a large-scale comprehensive motor manufacturer, it has strong technical capabilities and a high market share in the field of servo motors. Mitsubishi Electric's servo motor product line covers from the high-performance MR-J5 series to the classic MR-J3 series. The MR-J5 series is the flagship product of Mitsubishi Electric, supporting high-resolution encoders, multiple communication protocols, and offering various models that cover different power ranges and application needs. The MR-J4 series is an earlier high-performance product launched by Mitsubishi Electric, offering good cost-performance ratio and still has certain applications in the market.
The MR-J3 series provides a variety of types such as rotary servo motors, linear servo motors, and direct-drive motors to meet different application needs. The servo motors of the MR-J3 / MR-J4 / MR-J5 series all have the capability to control the operation and positioning of mechanical equipment components under high-speed, high-precision, and low-energy consumption driving methods, suitable for various industrial automation equipment, such as CNC machines, packaging machinery, food machinery, and industrial robots.
Siemens
Official website:
Siemens AG was founded in 1847, headquartered in Germany, and is a leading enterprise in the field of global electrical engineering, focusing on electrification, automation, and digitalization, which are the most promising growth areas. Currently, Siemens has launched three major series of AC servo motors: SIMOTICS S-1FK2, SIMOTICS S-1FL2, and SIMOTICS S-1FL6.
The SIMOTICS S-1FK2 series servo motors are known worldwide for their compact design, lightweight, easy tuning, and powerful torque output, using OCC single-cable technology, and are suitable for fields such as digital printing machinery, labeling machines, laser welding, and three-coordinate robots. The SIMOTICS S-1FL2 series servo motors, known for their small size, high speed, and high overload capacity, are suitable for industries such as batteries, electronics, packaging, and woodworking machinery. As the main push of Siemens, the SIMOTICS S-1FL6 series servo motors are renowned for their high dynamic performance, reliable operation, low cost, and ease of use. They are suitable for fields such as electronic assembly, metal forming, and material handling.04
FANUC
Official website:
Established in 1956 and headquartered in Japan, FANUC has been active in the field of factory automation since its inception, providing products including NC (numerical control), servos, and lasers, as well as robotic and intelligent machinery products that apply these foundational technologies. The FA (Factory Automation) division, which is based on FANUC's foundational technologies of numerical control and servo technology, is one of FANUC's three major divisions. FANUC has two product series in the servo motor field, the αi series and the βi series. The αi series of AC servo motors from FANUC is renowned for its high performance and precision, making it suitable for applications such as CNC machines, robots, and automated production lines. The βi series servo motors are known for their cost-effectiveness and are ideal for applications that are cost-sensitive yet still require good performance, such as in the fields of warehousing logistics, packaging machinery, and food machinery.
05
Panasonic Corporation
Official website: panasonic.cn
Founded in 1918 and headquartered in Japan, Panasonic Corporation's business spans a wide range of areas including consumer electronics, residential equipment, automotive systems, and industrial automation. Panasonic's servo motors are known for their reliability and precision. The market currently sees two main series of Panasonic servo motors: the MINAS A4 and MINAS A6. The MINAS A4 series, being the previous generation, may not be as advanced as the MINAS A6 series but still offers good performance and stability, suitable for most industrial automation applications. The MINAS A6 series of AC servo motors represents the latest generation from Panasonic Corporation, embodying high precision, high performance, and high stability. They are utilized in automated equipment such as robotic arms, CNC machines, and food processing machinery.06
AB B
Official Website: new.abb.com
AB B is a globally leading electrical engineering and automation technology group, headquartered in Switzerland. AB B's servo motor product line is very rich, and its diversified product portfolio allows for widespread application across multiple industries. Specifically, AB B has introduced several series of servo motors, including DSM, eSM, HDS, HY, MU, and more. The DSM series is a high-performance servo motor with a broad range of rated power and a rich output of torque, suitable for applications requiring high performance and flexibility. The eSM series is a high-dynamic servo motor, which, when used in conjunction with MicroFlex and MotiFlex series servo drives, can achieve an optimized combination of cost and performance. The HDS series combines high torque with low inertia, offering outstanding performance. The HY series is a high-performance explosion-proof servo motor, developed, designed, and manufactured in strict accordance with the highest explosion-proof standards, suitable for applications in areas with potential explosion hazards. The MU series of servo motors is primarily used for external axes of AB B industrial robots and is known for its high performance and stability.
07
B&R Industrial Automation
Official Website:
B&R Industrial Automation is an Austrian industrial automation technology supplier, established in 1979 and became a part of the AB B Group in 2017. B&R Industrial Automation has accumulated extensive experience in machine and factory automation and offers two product series in the field of servo motors, namely 8JS and 8WSA, with the 8JS series including two sub-series of servo motors, 8JSB and 8JSQ. The B&R 8JSB and 8JSQ series servo motors feature a hygienic design, enabling efficient and clean operation in food production and biomedical engineering scenarios. Additionally, their 8WSA series servo motors are capable of high-precision synchronization and precise positioning in confined spaces, suitable for applications such as dispensing systems, clamping devices, measuring and testing equipment, filling systems, and robotic arms.08
Beckhoff
Official Website:
Founded in 1980, Beckhoff is renowned in the field of automation technology and is one of the leading global suppliers of automation technology. Beckhoff's servo motor product line is quite extensive, covering the AM, AMP, and AMI series of rotary servo motors and the AL series of linear servo motors. The flagship AM series of synchronous AC servo motors features a single-cable technology and is known for its durability and high power, making it suitable for applications with stringent requirements for dynamics, speed, and performance. The AMP series is a synchronous AC servo motor integrated with a servo drive, designed for modular mechanical design solutions without a control cabinet. The AMI series is a synchronous DC servo motor integrated with a servo drive, designed for low-voltage range modular mechanical design solutions without a control cabinet. The AL series linear servo motors feature a modular coil design with extremely high magnetic density, suitable for compact drive technology.
09
Rockwell Automation
Official Website:
Rockwell Automation is a global leader in industrial automation and information solutions, headquartered in the United States and established in 1923. The company offers the LDC and LDL series of linear servo motors and the Kinetix VP, MPF, MPS, MPM, MPL, RDB, and HPK series of rotary servo motors. Their linear servo motors are primarily used in applications such as dispensing machines and solar panel scribing machines. The Kinetix VP series servo motors provide smooth integrated motion control through the EtherNet/IP network.
The Kinetix MPF series servo motors not only offer high efficiency and high torque capabilities but also features specifically designed to meet the unique demands of food and beverage applications, suitable for applications including food forming, filling, packaging, and sealing. The Kinetix MPS series is a stainless steel servo motor, capable of operating in high-pressure or highly corrosive washdown environments. The Kinetix MPM and Kinetix MPL series correspond to medium and low inertia servo motors, respectively. The Kinetix RDB series is a direct drive servo motor, which can be directly connected to the load without the need for gearboxes or other mechanical components. The Kinetix HPK is an AC asynchronous servo motor, featuring high power and precise positioning capabilities.10
Schneider Electric
Official website:
Schneider Electric, established in France in 1836, is one of the world's leading suppliers of energy management, industrial automation, and digital solutions. The Lexium series of servo motors from Schneider Electric are renowned for their stability, reliability, ease of use, and cost-effectiveness, making them suitable for automation equipment in industries such as logistics and warehousing, automotive manufacturing, and food and beverage. Specifically, the Lexium 32 series and LXM52 series are designed for applications requiring high performance and precise control. The Lexium 23Plus series and Lexium 26 series are suitable for applications requiring medium torque and cost-effectiveness. The Lexium BCH series, tailored for the Asian market, is ideal for applications that demand compact dimensions and cost benefits. The Lexium 18 series is suitable for applications that require high cost-performance ratio and simple control. The LXM62 series is also designed for applications that demand high torque density and precise control.
11
Bosch Rexroth
Official website:
Bosch Rexroth, a wholly-owned subsidiary of the Bosch Group, is headquartered in Germany and specializes in drive and control technology. In 2022, Bosch Rexroth acquired Elmo Motion Control, an Israeli motion control company, further strengthening its presence in the field of factory automation. In the field of electric drive technology, Bosch Rexroth is known for its high-performance servo motors and drive systems. The MSK series servo motors are suitable for blower units due to their wide power range and limited size increments. The MKE series is a flameproof, non-ventilated permanent magnet specialized servo motor suitable for potentially explosive environments. The MSM series is a maintenance-free synchronous AC servo motor, suitable for applications requiring long-term stable operation and low maintenance costs. The MAD series is an air-cooled asynchronous AC servo motor, and the MAF series is a water-cooled asynchronous AC servo motor; both series are suitable for applications that require high power output.12
Faulhaber
Official Website: faulhaber.com.cn
Faulhaber is a company specializing in micro and microdrive technology, established in 1947 and headquartered in Germany. Faulhaber offers a comprehensive range of micro and microdrive systems worldwide, from high-performance direct current (DC) motors to precision microdrives with an outer diameter of only 1.9 millimeters. Faulhaber's brushless DC servo motors are suitable for applications requiring high torque in a small space due to their miniaturization, high precision, high performance, and high reliability. For instance, the BX4 series brushless DC servo motors can be combined with various gearboxes and lead screws to provide drive solutions for industrial robot end-effectors, optical systems, and medical testing equipment. The BP4 series four-pole brushless DC servo motors boast extremely high torque and an outer diameter of only 22 to 32mm. The BXT SC series brushless DC motors come with an integrated speed control drive, and with the drive circuitry fully integrated, the motor's length is increased by only 6.2 mm. They can be combined with various precision gearboxes and are applied in fields such as pumps, handheld tools, equipment manufacturing, laboratories, and industrial automation.
13
Lenze Company
Official Website:
Lenze was founded in 1947 and is headquartered in Germany. For over seventy years, drive and automation systems have been at the core of its expertise. Lenze's MCS series synchronous AC servo motors are renowned for their high dynamic response and precise positioning, making them suitable for applications in textile machinery, packaging machinery, CNC machines, robotics, and semiconductor production equipment. The m850 series synchronous AC servo motors are compactly designed, easy to control, and run smoothly, making them suitable for applications that require moderate dynamic performance and strong driving force, such as positioning, robotics, and packaging technology, as well as handling systems. The MCA series asynchronous AC servo motors have the advantages of small size and low rotational inertia, making them ideal for compact units and environments that demand high structural-related operational stability. The SDSGA series of small servo motors feature a smooth surface, high reliability, and easy maintenance, making them suitable for hygienic environments. Additionally, their MQA series asynchronous AC servo motors offer high power and large torque output, making them suitable for the main drive of radial flow fans.14
OMRON Corporation
Official Website:
OMRON Corporation, established in 1933 and headquartered in Japan, began with the production of timers and protective relays and has gradually evolved into a global leader in automation control and electronic equipment manufacturing. The R88 series of servo motors is a major series of OMRON, which includes the R88M and R88L sub-series. Among them, the OMRON R88L is a linear servo motor characterized by high speed and high precision, suitable for conveyors, stackers, and other equipment that require smooth operation and precise positioning. The OMRON R88M series of AC servo motors covers various power ratings and sizes, equipped with real-time automatic tuning functions, which simplifies the gain setting process, making adjustments more convenient, and is applied in multiple industrial automation fields such as CNC machines, industrial robots, and automated production lines.
15
NIDEC CORPORATION
Official Website:
Comment